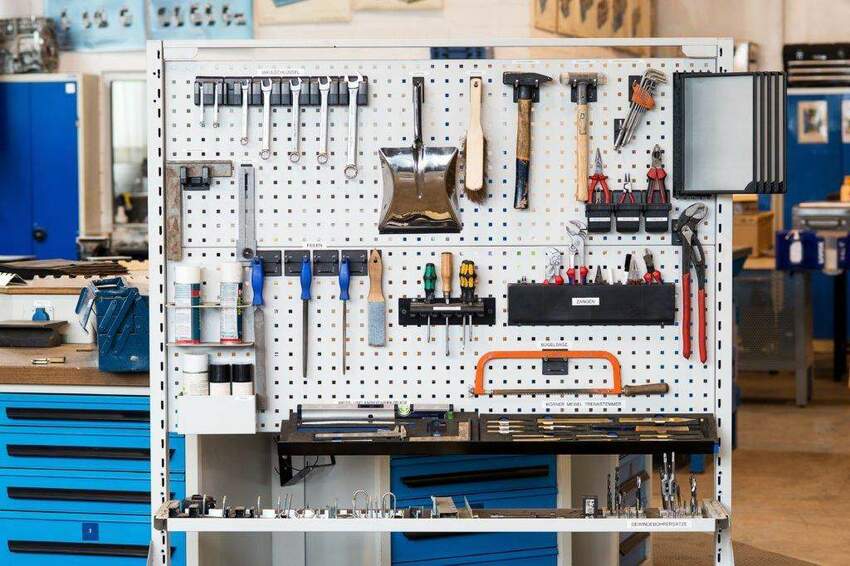
What is 5S? Companies adopting the lean production philosophy often implement the 5S process to bring order to the workplace and thereby support lean production.
Why Use the 5S Concept as a Model for Lean Supply Strategy? 5S is a proven model for organizing and maintaining a lean production environment. The relationship between purchasing or supply and the general management of operations may be improved through the use of a common vocabulary built around concepts familiar to the organizational head and the heads of other departments.
For this reason, 5S is an appealing model for the development of supply strategy in a lean production environment. A model for using 5S to develop supply strategy follows. Sort: Remove All But the Necessary Materials, Equipment and Supplies. Typically, the first step in a producer’s implementation of 5S will be a tour of the target area marking with red tags those items that appear out of place or unnecessary. After reviewing each item, the item will either be put in its proper place or removed if it is unnecessary or redundant.
The Sort process is essential to developing the organization of the workspace needed for lean production. Sorting the supply base includes selection of suppliers to add to the system and selecting suppliers to eliminate (supply base consolidation or rationalization). Implementing Sort in the supply base through supplier consolidation achieves the following benefits. It reduces the waste of inefficient work methods by reducing the number of suppliers that must be managed by the procurement staff.
Sorting reduces the waste of selecting the wrong suppliers by focusing efforts of selection, evaluation, and improvement on a few select suppliers. This also improves the quality (conformance to specifications and delivery) of the products received from these suppliers by focusing quality assurance, control and improvement activities on a smaller number of suppliers.
Sorting reduces processing waste as fewer purchase orders may be necessary and fewer selection audits are needed. Finally, Sorting increases the opportunity for supply chain partnering. So for the management of supply, the primary implementation of Sort is selection.
There are several criteria that may be used to identify candidates for elimination in the sorting process. First, a performance review (i.e., review of quality, delivery, and price performance) isolates some candidates for elimination. Next, a review of redundant suppliers is conducted. How many suppliers have identical or overlapping capabilities?
Finally, a review of the number of part numbers purchased from each supplier will often result in identification of a large number of suppliers providing only one or a few parts. All of the sorting or consolidation is an effort to approach an optimum number of suppliers. Multiplying suppliers increases variation and overhead.
The practice of utilizing multiple suppliers for a single part in order to reduce risk often increases risk, just as increasing the number of components in an assembly usually increases the probability of failure. Set in Order: Arrange Product and Equipment So It is Easy to Find and Easy to Use. Equipment and storage locations are labeled so equipment or tools will be easy to identify and put away when they are no longer in use (e.g., tool cutouts or outlines on a peg board or in a tool chest).
The labeling of storage locations with tape on the floor or the work station facilitates visual management. A glance is sufficient to identify missing tools or tools not properly stored. Arranging suppliers so they are easy to use brings to mind the concept of segmentation. Segmentation provides a “place for everything” and allocates “everything in its place.”
The supply base is sorted or segmented by value potential and risk, by strategic value and opportunity for cost improvement, by value potential and criticality, or other such criteria. The proper “place” for a supplier is a location in a segmentation matrix. The value of this exercise comes from clearly identifying how each supplier will be treated based on identifiable criteria.