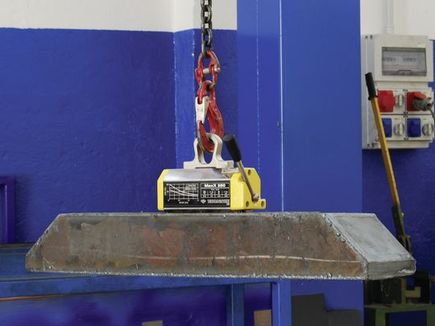
Służą do podnoszenia i przenoszenia ciężkich elementów magnetycznych z żelaza i stali . Urządzenia te nie wymagają żadnego zewnętrznego ani wewnętrznego zasilania. Włączanie i rozłączanie pola magnetycznego następuje w wyniku przestawienia ręcznej dźwigni.
Chwytaki magnetyczne, znane również jako magnesy dźwigowe, są niezależne od źródeł prądu, co korzystnie wpływa na ich bezpieczeństwo oraz energooszczędność pracy. Zawierają obwody magnetyczne zbudowane z wykorzystaniem wysokoenergetycznych magnesów stałych neodym-żelazo-bor (NdFeB).
Łożyskowana ręczna dźwignia ustawia odpowiednio magnesy stałe w obwodzie magnetycznym. Następuje wtedy wzmocnienie lub osłabienie (do wartości resztkowych) pola magnetycznego na powierzchni roboczej chwytaka. Podnoszony element zamyka obwód magnetyczny, zwierając dwa bieguny magnetyczne „N” i „S”.
Dzięki swoim niewielkim rozmiarom i stosunkowo małej wadze, są bardzo wygodne i łatwe w obsłudze. Znajdują zastosowanie w składach stali, fabrykach, magazynach, warsztatach, dokach i wszędzie tam, gdzie mogą być pomocne przy przenoszeniu blach, płyt i innych dużych stalowych elementów.
Rzeczywisty udźwig każdego chwytaka (inaczej magnesy do zawiesia) zależy od następujących czynników:
- grubości i kształtu podnoszonych elementów - dla cylindrycznych elementów pełnych (walców, prętów) udźwig nominalny jest o około 50% mniejszy. Minimalna grubość podnoszonych przez chwytak CM70 elementów wynosi 1,5 mm;
- wielkości szczeliny powietrznej między powierzchnią chwytaka a podnoszonym elementem;
- gatunku podnoszonej stali (im większa zawartość żelaza, tym większy udźwig: współczynnik wydajności udźwigu dla stali niskowęglowych to 1,00; dla stali wysokowęglowych - 0,90; dla stali niskostopowych - 0,75; dla żeliwa 0,50);
- temperatury otoczenia i temperatury podnoszonych elementów (nie może być wyższa niż 80 stopni Celsjusza).